Why in the News?
The Indian Space Research Organisation's CE20 cryogenic engine passed a critical sea-level test, a breakthrough in its propulsion technology.
More about the news
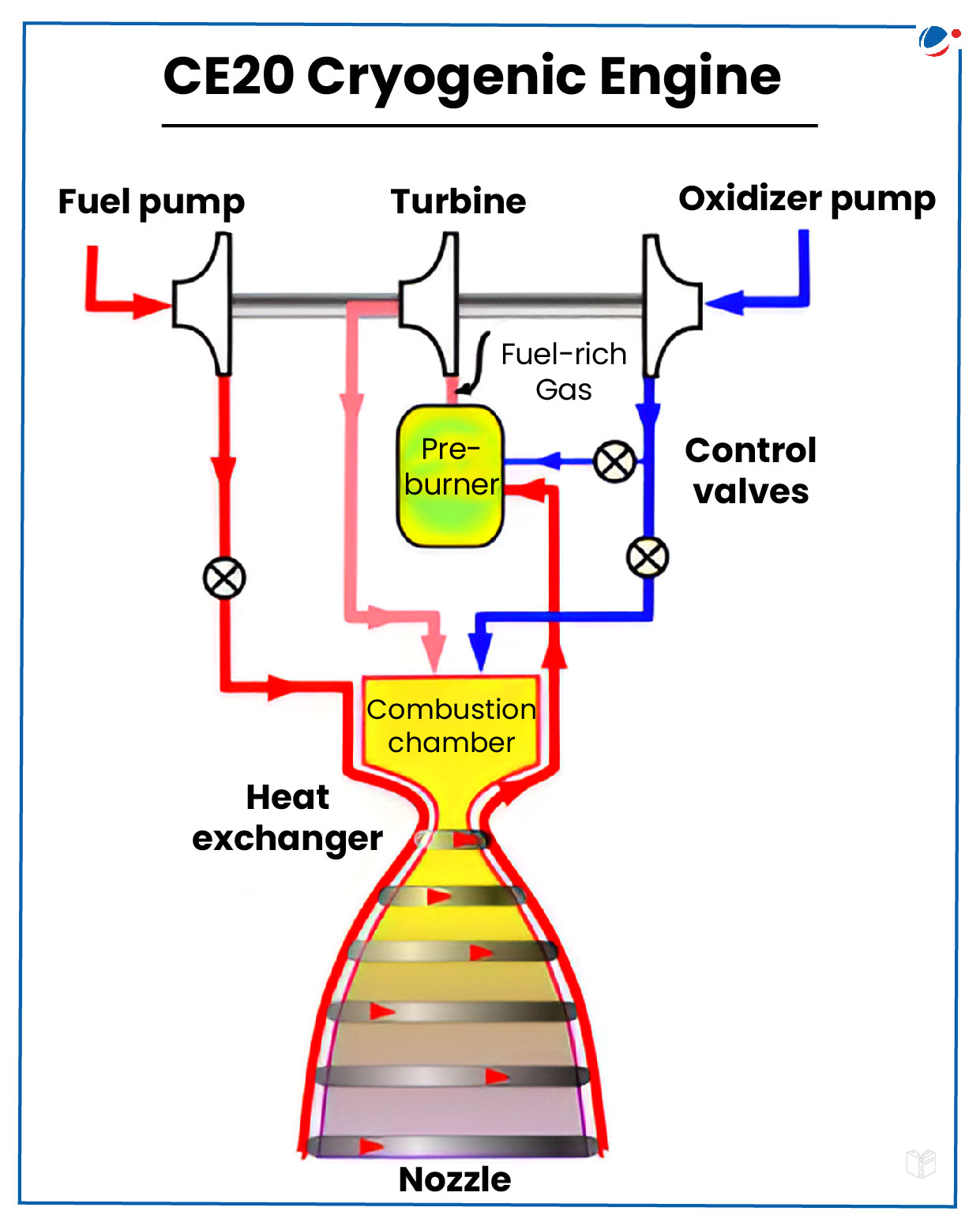
- The sea-level test implemented a 'Nozzle Protection System' to manage issues like flow separation within the nozzle, which can cause vibrations, thermal problems, and potential damage.
- ISRO has been working on the engine in view of its Gaganyaan mission, India's first manned spaceflight.
- Test Location: ISRO Propulsion Complex in Mahendragiri, Tamil Nadu.
- The sea-level test introduced an innovative 'Nozzle Protection System' to address technical challenges in engine restart capability.
- Earlier, HAL had also established the Integrated Cryogenic Engine Manufacturing Facility in Bengaluru, 2023.
How does a cryogenic engine work?
- The working principle: The thrust is produced by an internal combustion/pressure difference.
- This follows Newton's Third law of motion- "Every action has an equal and an opposite reaction".
- Uses: Cryogenic engines are used in space launch vehicles, in the last stage (or upper stage) of a rocket.
- A Cryogenic engine uses both cryogenic fuel and oxidizer, liquefied at a very low temperature.
- Fuel: The fuel and oxidizer used in a cryogenic engine are liquefied gases, stored at extremely low temperatures.
- Generally liquid hydrogen liquefied at -253° Celsius is used as fuel and liquid oxygen liquefied at -183° Celsius is used as oxidizer.
Note: Semi-cryogenic engine uses refined kerosene instead of liquid hydrogen which offers advantages of lighter weight and storage at normal temperature.
Advantages of cryogenic engine
- Efficiency and Thrust: Compared to solid and earth-storable liquid propellant rocket stages, cryogenic propulsion offers superior thrust, with LOX+LH2 producing maximum energy and lightweight water vapor, resulting in higher performance.
- Fuel Efficiency: Cryogenic engines use less fuel. ISRO's PSLV Vikas engine burns 3.4 kg/sec, while cryogenic engines need only 2 kg/sec for the same thrust. Their specific impulse reaches 450 seconds versus 260 seconds for solid propellants.
- Eco-Friendly Technology: Hydrogen-oxygen combustion emits only steam, making cryogenic propulsion a clean, carbon-free solution.
- Heavy Payloads & Space Missions: High efficiency makes cryogenic fuel ideal for heavy payloads and long missions like Gaganyaan and Chandrayaan.
Some of the challenges in Cryogenic engine technology
- Complex technology: A very complex system compared to solid or liquid propellant stages due to its use of propellants at extremely low temperatures and the associated thermal and structural problems.
- High thermal gradient and thermal stresses: Problems such as cracks forming on the divergent outer shell, sudden stoppage of rotation, blockages in the channels, distortions in nozzles etc.
- High Operational Pressures: The high operational pressures of thrust chamber coolant circuits and thrust related stresses typically require high strength super alloys for load reaction, ultimately a major engine weight driver.
- Maintaining low temperature: The most significant thrust chamber challenge is balancing system performance with the thermal capability of coolant liners at deep throttle; low coolant flow operation.
- High cost of development: Cryogenic Upper Stage (CUS) project in 1994 had budget of Rs 300 crore.
About CE20
- Developed by: The Liquid Propulsion Systems Centre (LPSC), Valiamala, Kerala.
- Output: It has been upgraded to produce a thrust level of 20 tonnes. Apart from that, it is capable of producing an enhanced thrust of 22 tonnes for the C32 stage in the future.
- C32 is new and heavier cryogenic upper stage called C32, a variant of the C20 engine that will replace lesser capacity C25 stage.
- Successful Mission: It has demonstrated its capability by successfully operating in six successive LVM3 missions, including the Chandrayaan-2, Chandrayaan-3, and two commercial OneWeb missions.
- LVM3 (Geosynchronous Satellite Launch Vehicle Mk III) is three-staged vehicle, capable of lifting 4000kg payload.
Cryogenic Engine comparison with other engines
Characteristics | Cryogenic Engine | Jet Engine | Solid Propellant Engine | Liquid Propellant Engine |
Air Intake | No air intake is required. | Air intake is required. | Air intake is required as oxidizer. | Air intake is required as oxidizer. |
Fuels | Generally super cooled Hydrogen and Oxygen. | (Jet A-1, kerosene), Kerosene-gasoline mixture, Aviation gasoline (avgas), Bio-kerosene. | Fuels for composite propellants are generally metallic powders, with aluminum being the most common. | Hydrazine, mono-methyl hydrazine (MMH), unsymmetrical dimethyl hydrazine (UDMH) etc. |
Fuel temperature | The temperature of fuel must be Very low. | Fuel storage does not require low temperature. | Fuel storage does not require low temperature. | Fuel storage does not require low temperature. |
Efficient working | It runs efficiently when low temperature fuel transforms and mixes correctly and ignites. | It runs efficiently at supersonic speed that forcefully compresses air before combustion. | It runs efficiently when fuel is provided with sufficient oxidizer. | It runs efficiently when fuel is provided with sufficient oxidizer. |
Purpose | Third stage/ last stage of rocket. | Used in the Airplanes etc. | Used as boosters in initial liftoff. | Act as main stage of rocket after booster separation. |
Conclusion
The CE20 Cryogenic engine marks a significant milestone in ISRO's progress with cryogenic technology. Advancing further, ISRO could explore start fuel ampules like Tri-ethyl-aluminum and Tri-ethyl-boron to enhance ignition reliability and efficiency.